Specialist Suggestions on What is Porosity in Welding and Just How to Resolve It
Specialist Suggestions on What is Porosity in Welding and Just How to Resolve It
Blog Article
Porosity in Welding: Identifying Common Issues and Implementing Finest Practices for Prevention
Porosity in welding is a prevalent problem that usually goes unnoticed until it triggers substantial problems with the integrity of welds. This common defect can compromise the stamina and sturdiness of bonded frameworks, posing security threats and resulting in pricey rework. By comprehending the source of porosity and executing efficient prevention techniques, welders can considerably improve the top quality and integrity of their welds. In this conversation, we will certainly discover the essential elements contributing to porosity formation, analyze its destructive results on weld efficiency, and talk about the very best practices that can be adopted to decrease porosity event in welding procedures.
Usual Root Causes Of Porosity
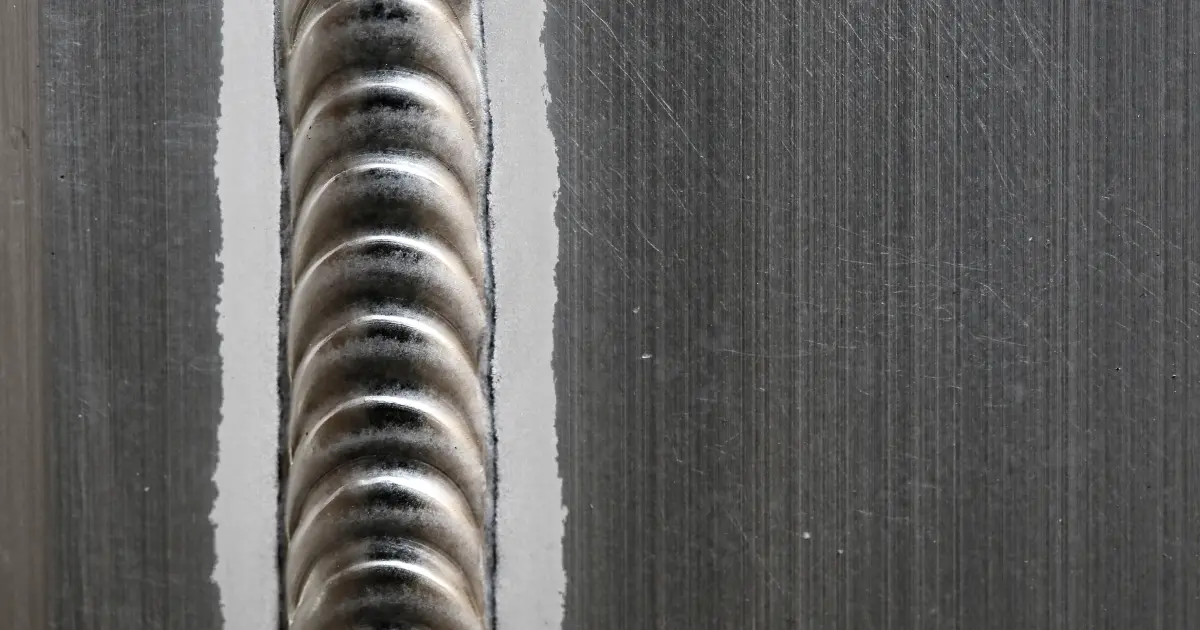
Utilizing unclean or wet filler products can present pollutants right into the weld, contributing to porosity problems. To mitigate these common reasons of porosity, detailed cleaning of base metals, correct shielding gas choice, and adherence to optimal welding specifications are crucial practices in achieving premium, porosity-free welds.
Influence of Porosity on Weld Top Quality

The existence of porosity in welding can considerably compromise the structural honesty and mechanical buildings of bonded joints. Porosity produces spaces within the weld metal, weakening its total stamina and load-bearing capability.
Welds with high porosity levels often tend to show lower effect strength and lowered capability to deform plastically prior to fracturing. Porosity can impede the weld's capability to successfully transmit pressures, leading to premature weld failing and potential safety and security hazards in vital frameworks.
Ideal Practices for Porosity Avoidance
To enhance the structural integrity and top quality of bonded joints, what details measures can be implemented to minimize the occurrence of porosity during the welding procedure? Making use of the right welding method for the certain material being welded, such as changing the welding angle and gun placement, can better stop porosity. Routine evaluation of welds and instant removal of any type of problems identified throughout the welding procedure are Home Page vital methods to avoid porosity and generate premium welds.
Relevance of Correct Welding Techniques
Applying proper welding strategies is paramount in making sure the architectural integrity and high quality of bonded joints, building upon the foundation of efficient porosity avoidance steps. Too much warm can lead to increased porosity due to the entrapment of gases in the weld swimming pool. Furthermore, making use of the suitable welding criteria, such as voltage, present, investigate this site and travel speed, is critical for accomplishing audio welds with marginal porosity.
Additionally, the option of welding procedure, whether it be MIG, TIG, or stick welding, need to align with the specific demands of the task to make sure ideal outcomes. Proper cleansing and preparation of the base steel, along with choosing the right filler material, are additionally crucial components of skilled welding strategies. By sticking to these ideal practices, welders can minimize the risk of porosity formation and create top notch, structurally audio welds.
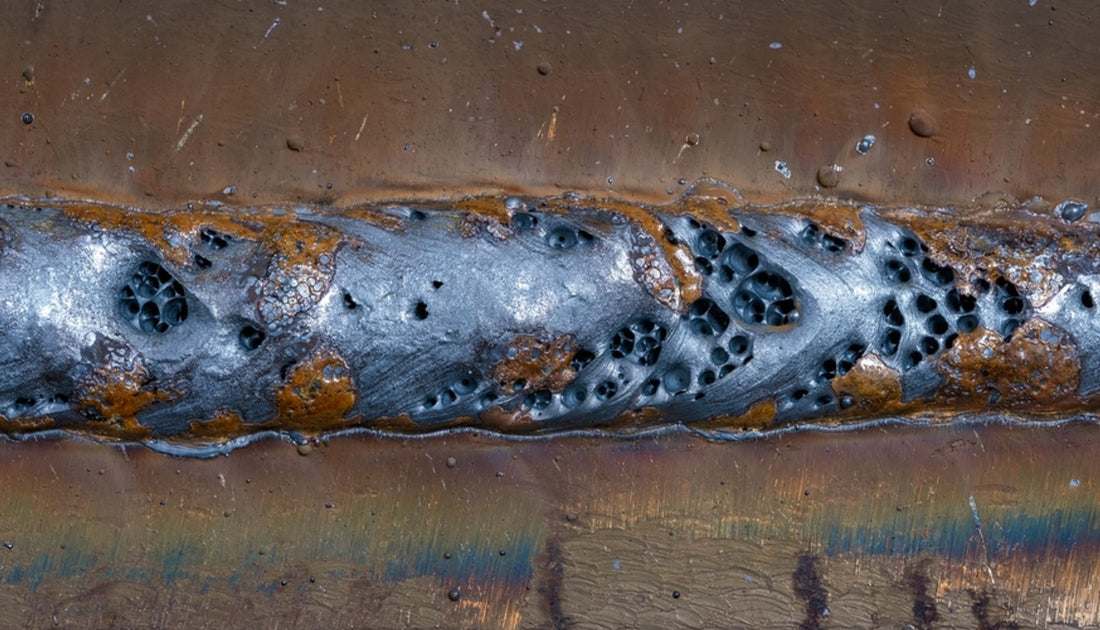
Testing and High Quality Control Actions
Examining treatments are important to identify and prevent porosity in welding, ensuring the strength and sturdiness of the last product. Non-destructive testing methods such as ultrasonic testing, radiographic testing, and aesthetic examination are generally utilized to determine prospective defects like porosity.
Conducting pre-weld and post-weld inspections is additionally important in preserving quality control standards. Pre-weld examinations include verifying the products, devices settings, and sanitation of the work area to protect against contamination. Post-weld inspections, on the other hand, evaluate the final weld for any kind of problems, consisting of porosity, and verify that it meets defined standards. Applying an extensive quality control strategy that includes thorough testing treatments and inspections is critical you can try these out to decreasing porosity concerns and guaranteeing the total quality of welded joints.
Verdict
To conclude, porosity in welding can be an usual problem that influences the top quality of welds. By identifying the typical reasons of porosity and applying best practices for prevention, such as appropriate welding techniques and screening steps, welders can ensure high top quality and reputable welds. It is important to focus on prevention methods to reduce the incident of porosity and preserve the integrity of bonded structures.
Report this page